曲げ加工とは?基本原理や加工の種類、メリット・デメリットを紹介
曲げ加工とは、金属やプラスチックなどの板材や棒材を、一定の角度や形状に変形させる加工方法のことです。主にプレス機やベンダー(曲げ機)を用いて、指定された曲げ角度や曲率半径を実現します。特に、板金加工や機械加工の分野では重要な加工方法の一つであり、自動車、航空機、建築、電子機器など、幅広い産業で使用されています。
曲げ加工の基本原理
曲げ加工は、材料に外力を加えることで、塑性変形(永久変形)を起こし、意図した形状に成形する技術です。曲げられた部分には、内側には圧縮応力、外側には引張応力が生じます。 曲げ加工の基本的な要素は以下の通りです。
- 曲げ半径(R):曲げ加工後の内側の半径
- 曲げ角度(θ):材料が曲げられる角度
- 板厚(t):曲げ加工前の板材の厚み
- 曲げ長さ(L):曲げ線の長さ(曲げる範囲の長さ)
曲げ加工を行う際には、材料の弾性回復(スプリングバック)を考慮し、適切な補正が必要です。通常、スプリングバックを補正するために、曲げ角度を意図した角度よりも2〜5°大きめに設定します。高張力鋼やアルミニウム合金では、さらに大きな補正が必要になることがあります。
曲げ加工の種類
曲げ加工にはさまざまな種類があり、それぞれの方法には特徴があります。
V曲げ
V字型の金型を用いて、板材を押し込んで曲げる方法です。Vダイの開口幅を調整することで、さまざまな曲げ角度に対応できます。代表的なプレスブレーキ(ベンダー)を用いる加工方法の一つです。
L曲げ(エッジベンディング)
板材の端を直角(90度)や任意の角度に曲げる方法です。L字型の部品やフランジ部品の成形に適しています。
U曲げ
U字型に曲げる加工方法です。深い曲げが必要な場合に使用され、パイプ形状の部品などに応用されます。
Z曲げ
Z字型に板材を曲げる加工方法です。薄板の金属製品や機械部品に用いられることが多いです。
ロール曲げ
3本のロールを使用し、材料を徐々に曲げながら円弧状に成形する方法です。円筒形状の部品や大型の曲げ加工に適しています。
曲げ加工における重要な要素
スプリングバック
曲げ加工後に材料が元の形に若干戻る現象を指します。特に高張力鋼やアルミニウム合金では顕著に現れ、 以下の方法で補正が行われます。
- オーバーベンド:意図した角度よりもやや強く曲げる
- リリーフ曲げ:曲げた後に追加の力を加えて弾性回復を抑える
- 型の選定:スプリングバックを考慮した金型の使用
材料特性と板厚
板厚が増すと、曲げに必要な力が大きくなり、最小曲げ半径(R)が大きくなります。一般的に、板厚の倍程度の曲げ半径を確保することが推奨されます。また、圧延方向(繊維方向)に対して直角に曲げると、割れが生じやすいので注意が必要です。
曲げ加工に用いられる機械
プレスブレーキ(ベンダー)
板金加工で最も一般的に使用される機械で、上型(パンチ)と下型(ダイ)の間に板材を挟み込み、圧力をかけて曲げる機械です。
ロールベンダー
ロールを回転させながら板材や棒材を曲げる機械で、大型の円弧状加工やパイプ製作に使用されます。
スイング曲げ機
曲げアームを用いて、板材を特定の角度まで持ち上げて曲げる方式で、比較的ソフトな曲げ加工に適しています。
曲げ加工に適した材料
- 鉄(SPCC, SPHC):一般的な板金加工に使用
- ステンレス(SUS304, SUS430):耐食性が高いが、スプリングバックが大きいため補正が必要
- アルミニウム(A5052, A6061):A6061は硬くて割れやすく、A5052の方が曲げ加工に適している
- 銅(C1100):加工しやすいが、加工硬化しやすいため、連続曲げには注意が必要
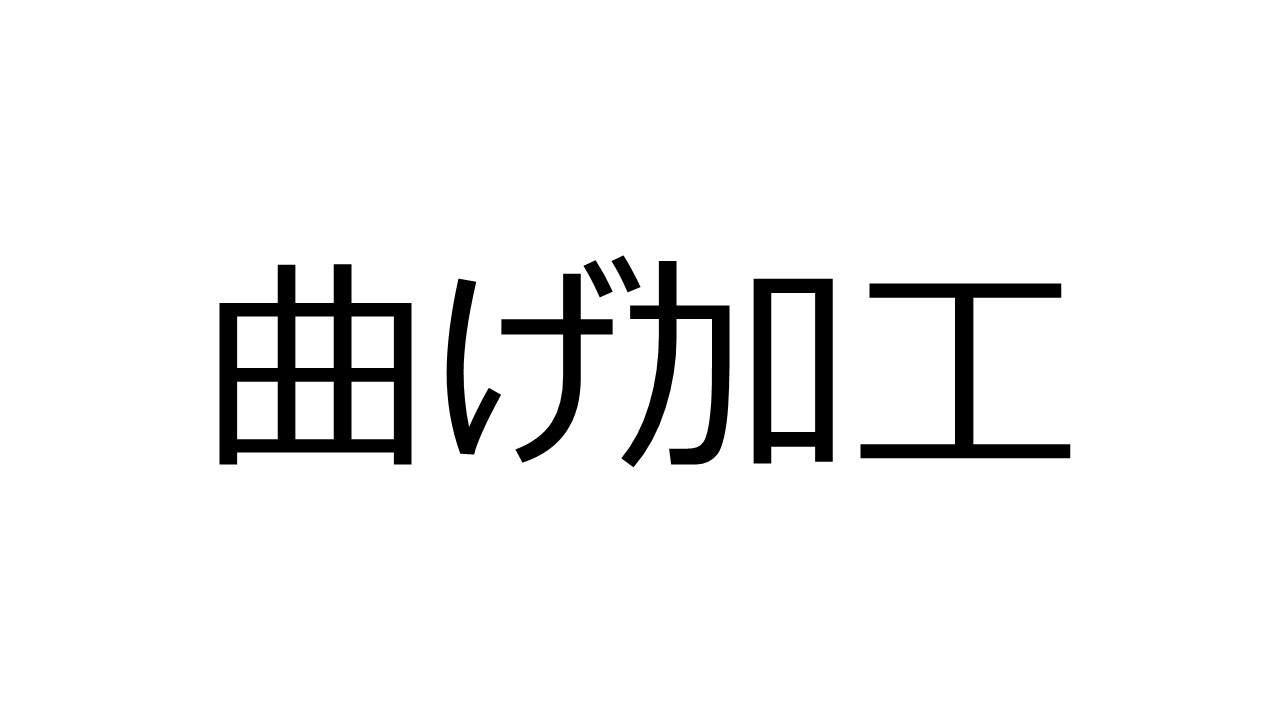
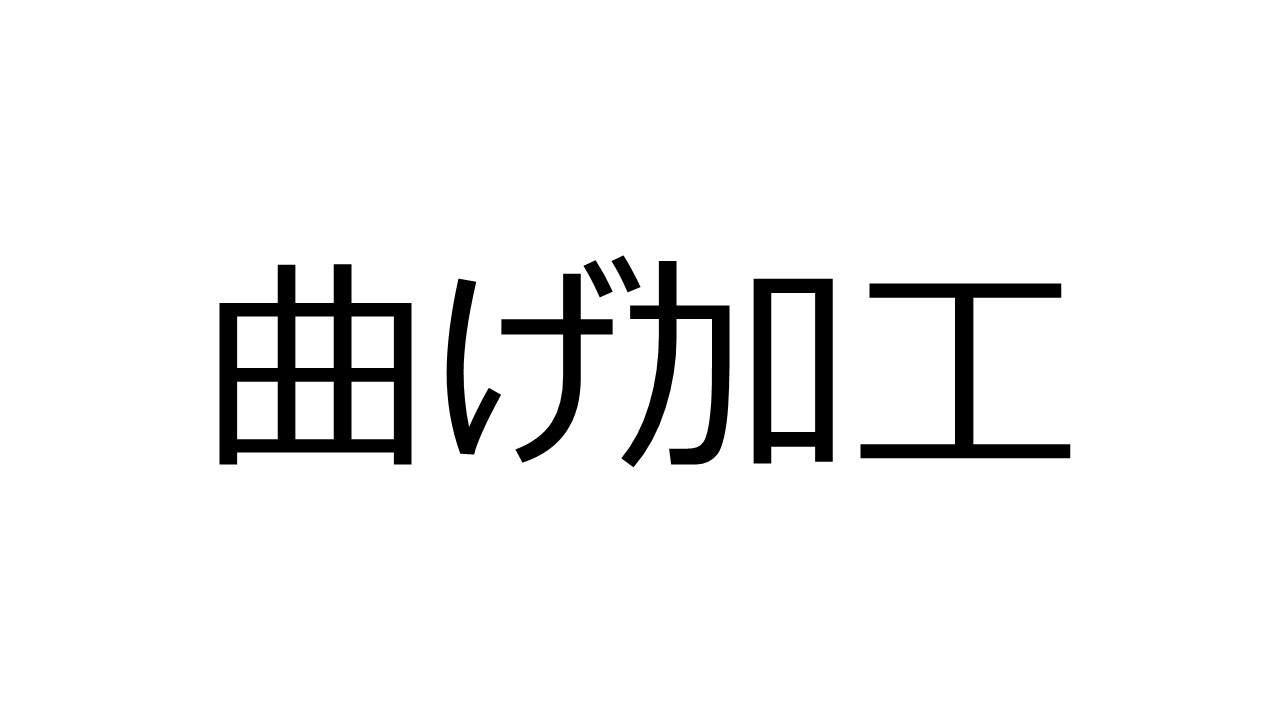
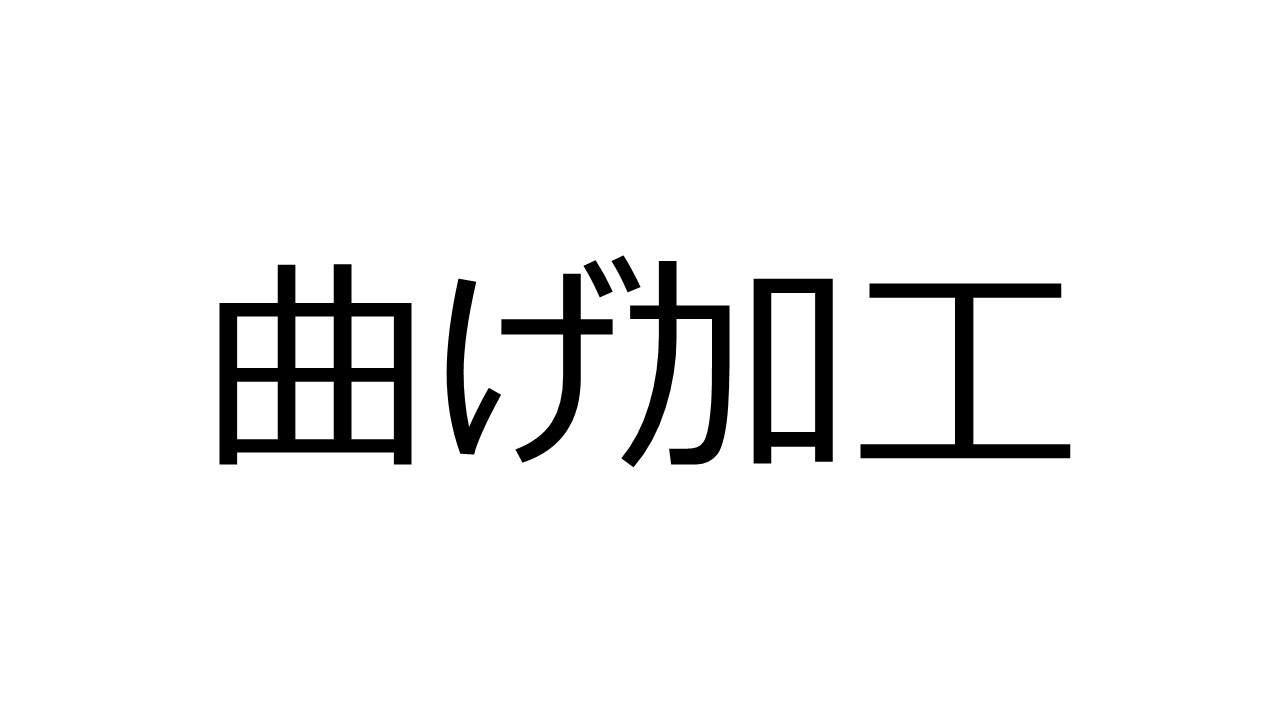
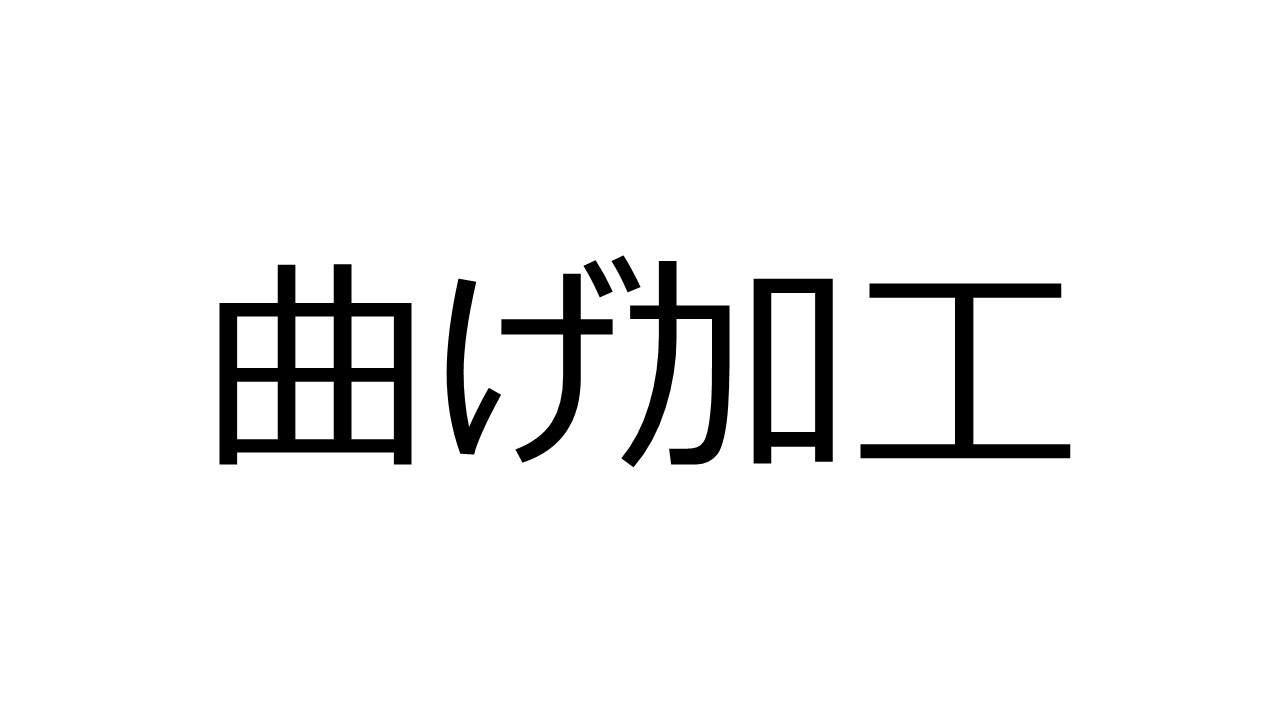
曲げ加工の利点と欠点
利点
- 加工コストが低い:切削加工に比べて材料の無駄が少なく、コストを抑えられる
- 大量生産に向いている:プレスブレーキを用いることで高精度な量産が可能
- 機械的強度が向上:溶接や接合よりも一体成形できるため、強度が確保しやすい
欠点
- スプリングバックの影響:弾性変形の影響で寸法精度を出しにくい
- 繊維方向による影響:圧延方向と直角に曲げると割れやすい
まとめ
曲げ加工は、金属材料の成形において不可欠な技術であり、さまざまな製品に応用されています。加工時にはスプリングバックや材料の特性を考慮し、最適な曲げ条件を設定することが重要です。プレスブレーキやロールベンダーなどの機械を駆使し、精度の高い加工を行うことで、高品質な製品を効率的に製造できます。